The Facility
The SAGD Facility is called “Orion” and consists of 4 major processes: Steam Generation, Injection/Recovery Wells, Deoiling and Water Purification, for recovery of oil. Aquatech will be working alongside Shell Canada (formerly BlackRock Ventures), the developer and IMV Projects, the integration engineers.
Project Overview
SAGD (Steam Assisted Gravity Drainage) is a technique to recover bitumen from the oil sands formation. The oil is recovered by further processing and upgrading the recovered bitumen. These formations are called Oil Sands as the bituminous resource is mixed with sand in the formation. The liquid that is pumped to the surface is a mixture of oil and water. The mixture is separated to a predominantly oil and water fractions in the deoiling process. From there, the oil fraction is sent to upgrader and refineries for conversion into a saleable product. The water fraction is sent to the Aquatech system for purification and reuse in the facility. Once purified, the water is used as feed to the boiler for generation of Steam for injection into the formation and the cycle continues.
Aquatech’s evaporator systems are a good fit for the SAGD process due to the high distillate purity (less than 5ppm non-volatile TDS). The high purity allows the water to be sent to a high pressure boiler for steam injection. In general, the higher the boiler pressure, more stringent the boiler feed water requirements.
Aquatech employs a proprietary vapor scrubbing system to meet the low level requirements of non-volatile inorganic and organic contaminants in the distillate to make it suitable as feed to the high pressure drum type boilers. Aquatech’s technology also makes this a green process by significantly reducing the water footprint. The evaporators recycle and purify between 96%-99% of the produced water generated in the facility. The SAGD facilities have a very high water demand, thus stressing the available fresh water resources in the region. This emphasizes the need for the oil sands industry in Alberta to recycle their water to minimize fresh water consumption.
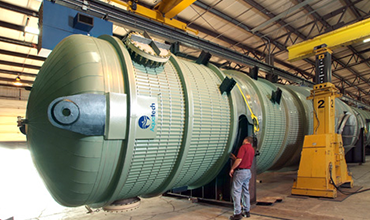
Scope of Service
The solution offered is a fully integrated and automated Evaporator system using MVC (Mechanical Vapor Compression) technology. The system is designed to operate the evaporators in series, such that the blow down from Evaporator 1 is the feed to Evaporator 2. The feed water to the first evaporator is a combination of boiler blowdown, brackish water, and produced water effluent from the plant deoiling process. The complete evaporation system is designed to treat 1000 gpm of combined wastewater on a continuous basis, where 500 gpm of distilled water is produced from each evaporator. This high purity distillate is returned to the boiler feed water tank for reuse in the SAGD process. Distillate that does not meet the purity requirement is sent to the Deoiled Water Storage Tank for reprocessing. The system is designed for semi-automatic start-up, automatic continuous operation, and automatic shutdown into a hot stand-by condition. The produced water from the SAGD process contains low hardness, high silica and high Total Organic Carbon (TOC). The feedwater chemistry will also contain an amount of calcium hardness. Calcium salts readily precipitate when concentrated in an evaporator and will scale the heat transfer tubes reducing the efficiency of the evaporator. A chemical conditioning system is supplied to condition the low solubility calcium carbonate into the more soluble hydrated lime and a dispersant type anti-scale is added to keep the calcium suspended. A chemical wash system has been provided to remove scale deposits from the evaporator. The ultimate concentration achievable by any Evaporator is limited by the boiling point elevation of the brine. The maximum TDS used in the design of the Evaporator is 13% based on the design chemistry. The brine discharged from the Evaporators is pumped for off-site disposal.
Design FGD Wastewater Analysis
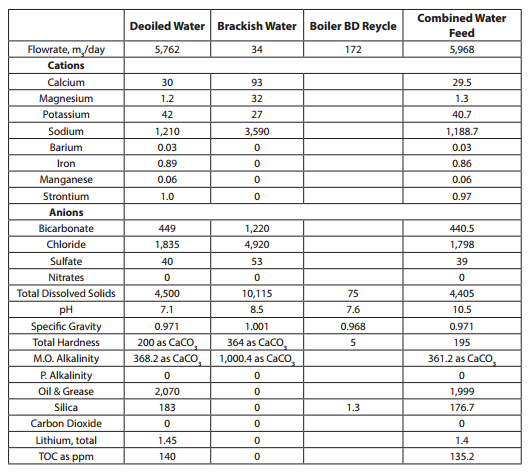