The Facility
The client, TCI Sanmar Chemicals S.A.E., located in Egypt, is one of the largest producers of chemicals in the MENA (Middle East & North Africa) region. TCI has a state-of-the-art chemical manufacturing facility at Port Said, for manufacturing 200,000 TPA of PVC (Polyvinyl Chloride) and 275,000 TPA of caustic soda. These are the largest capacities in the MENA region. In Phase 2 of the project, the PVC capacity has been doubled and a new calcium chloride granule plant added.
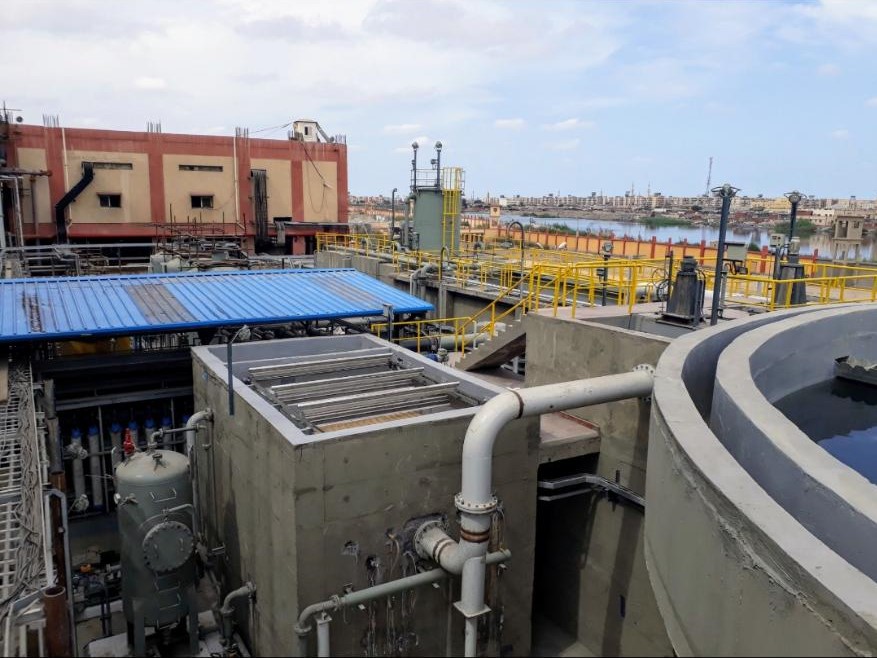
Since Egypt is water scarce, minimum discharge of effluent is expected of industrial plants. This requires provision of effluent recycle and reuse facilities in all industries in Egypt.
For its facilities in phase 1, TCI Sanmar had given the responsibility of the recycle plant to Aquatech based on extensive experience globally. Aquatech supplied a HERO™ (High Efficiency Reverse Osmosis) technology based wastewater treatment, recycle and Zero Liquid Discharge (ZLD) plant. The HERO™ system is designed and operated to achieve high recovery up to 90% in the most difficult of effluents, thus resulting in maximum recycle and minimum waste for disposal. HERO™ is a robust system ideal for difficult wastewaters, where every other contaminant in the effluent is a potential for operational problems in the conventional RO system. HERO™ system thus prevents the mandatory downtimes in day to day operations. The treated water from the Aquatech supplied system is over 90%, and is being recycled back to process and utilities.
The Challenge
When TCI Sanmar expanded for phase 2, they looked to Aquatech again for a solution. In phase 2, out of the various wastewater streams to be treated, the Poly Vinyl Chloride (PVC) effluent posed a real challenge. The effluent generated from the PVC manufacturing process carries large amounts of suspended solids consisting of very fine submicron sized PVC particles that are difficult to separate and remove by conventional methods. They don’t easily settle by coagulation, flocculation and clarification and easily get carried through the pre-treatment and disturb the performances of the ZLD mainstream units. Once these submicron particles enter the downstream units, particularly membranes, they cannot be removed by a chemical cleaning process and reduce the overall plant productivity.
Aquatech Solution
Pilot Study
Due to the submicron size of the PVC particle and its unique characteristic, Aquatech conducted a pilot on the effluent stream at the TCI Sanmar site using a combination of settling and flotation followed by membrane filtration in order to achieve efficient separation of the particles from water.
The objective of the pilot plant study was to:
- Study the performance of Dissolved Air Flotation (DAF) and different ultrafiltration (FU) membranes.
- Establish the best suited coagulant and coagulant aid in the given pre-treatment scheme for reduction of maximum solids and reduction of load to the downstream UF.
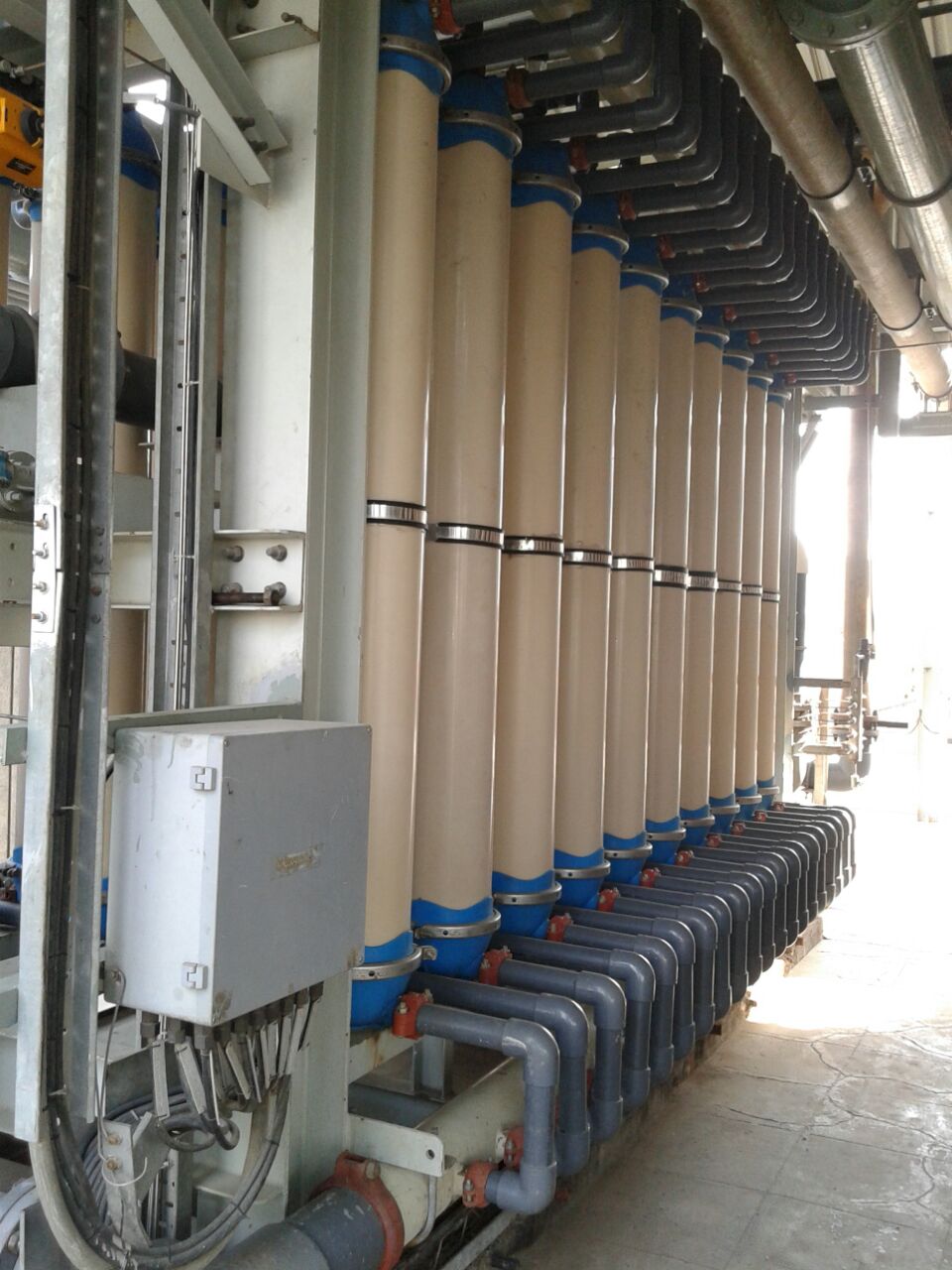
The pilot was successful and the results effectively demonstrated that the PVC non degradable contaminants could be removed by the selected DAF-UF scheme at source without further contaminating the ZLD main stream. The UF membrane selected was the QSEP membrane, as the most optimal solution to safeguard the downstream system from submicron sized particles. Q-SEP significantly increases the life of the RO membranes and reduces cleaning frequencies, thereby reducing operating expense for the RO system and improving the performance and productivity of the downstream RO units. Aquatech was then contracted to design, supply, and commission the system for the client.
Final Scheme
Based on the pilot results, the following scheme was designed by Aquatech, ultrafiltration being the main differentiator from the earlier scheme.
- Solid Contact Clarifier
- Dissolved Air Flotation
- Ultrafiltration (UF)
- HERO Pretreatment
- HERO Block
The plant has been supplied and implemented and was successfully commissioned in January 2019.
Water Analysis
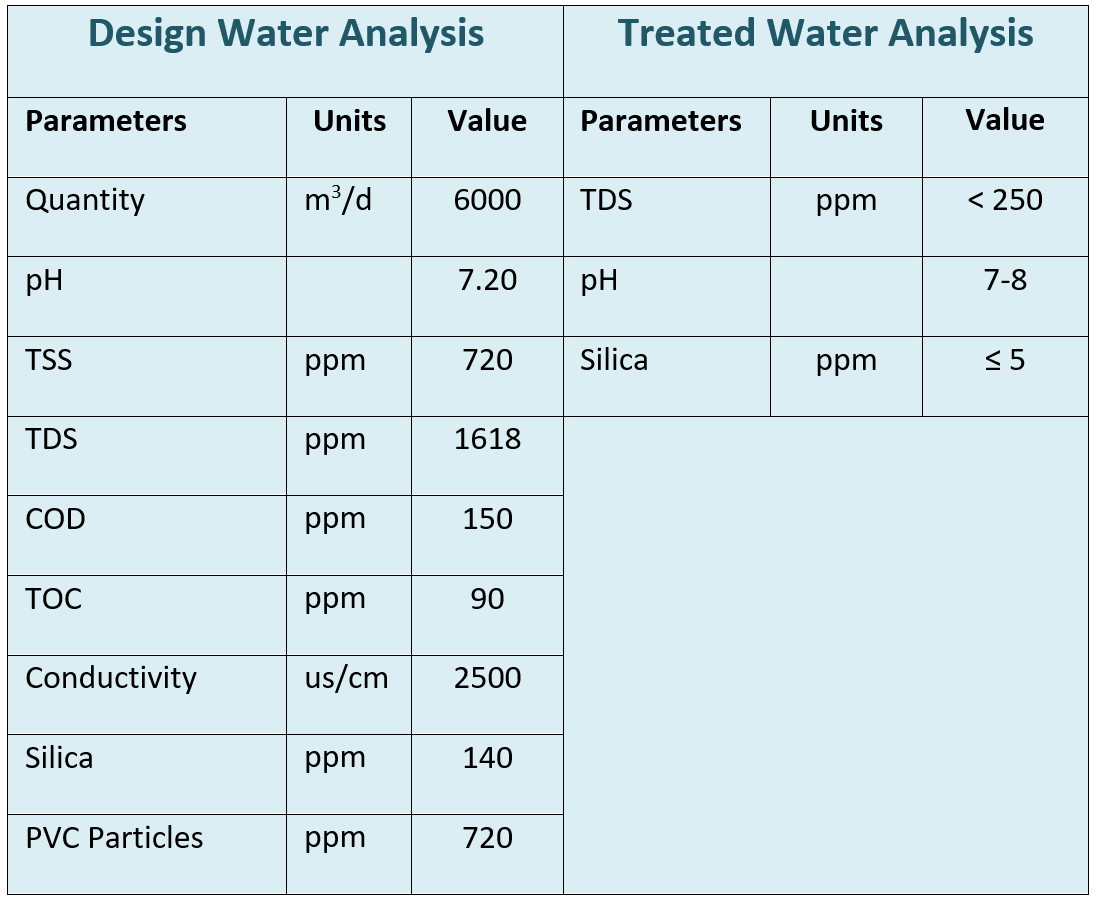
Process Flow Diagram
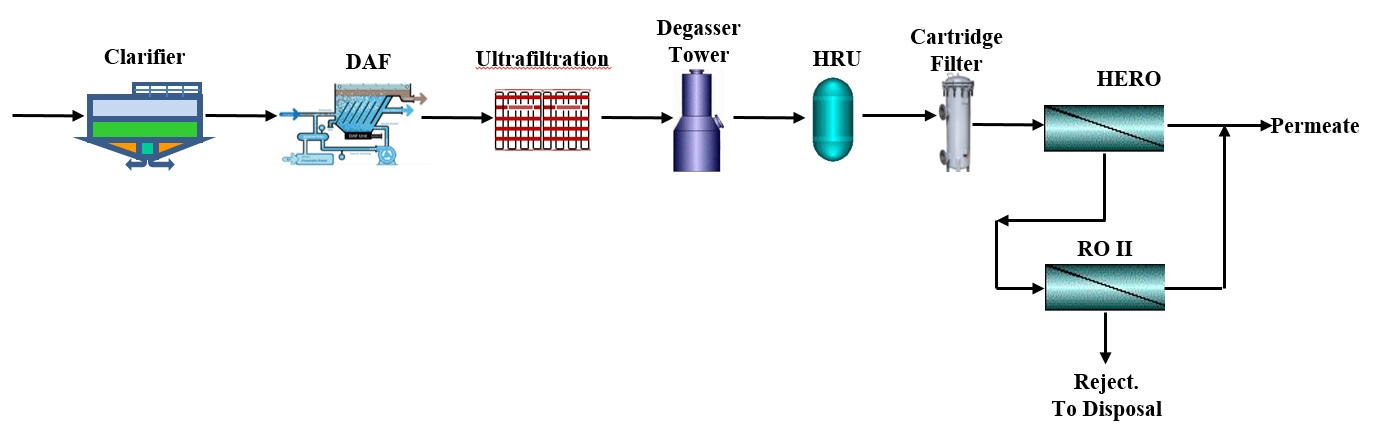