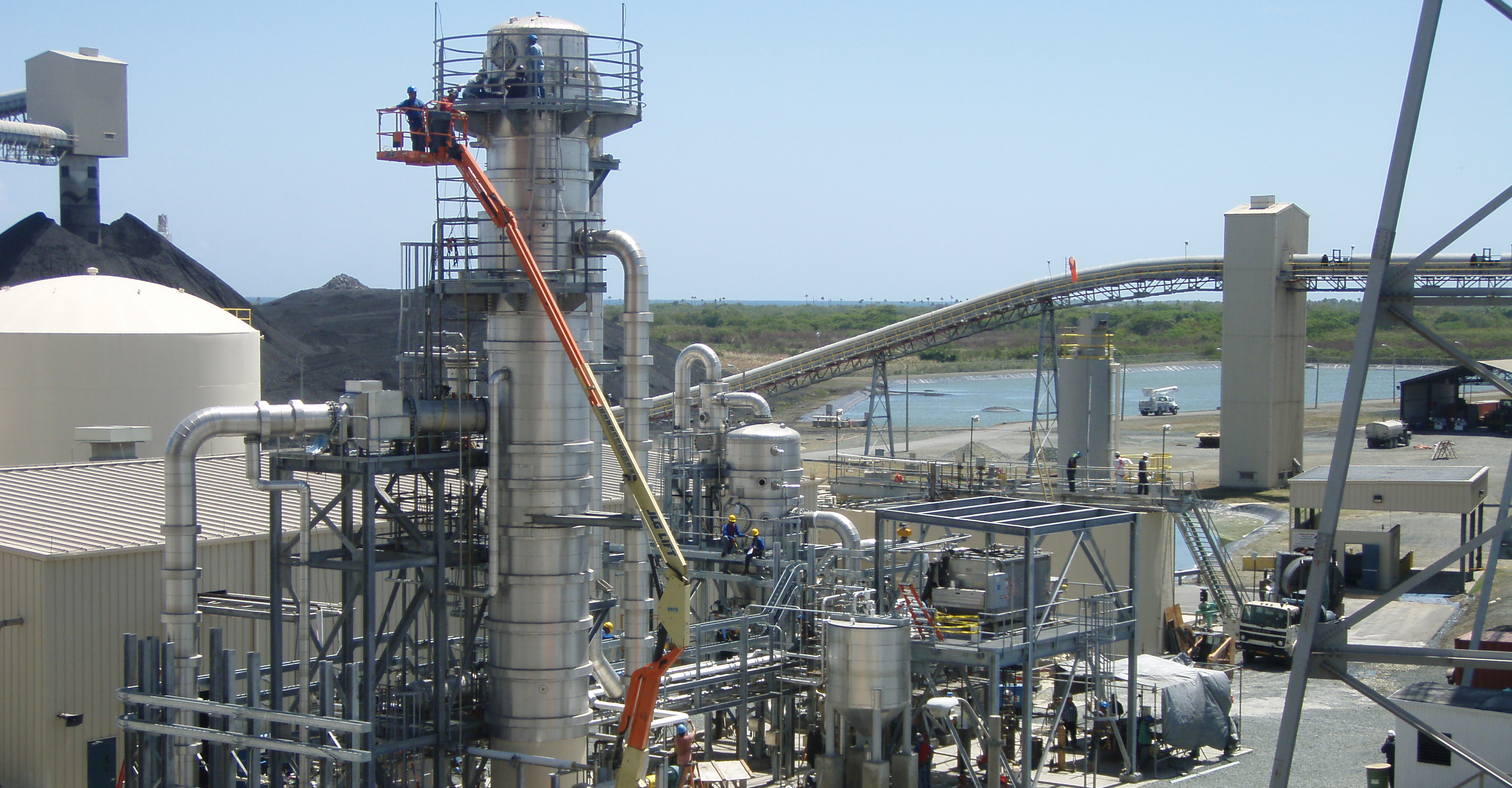
The Facility
AES Puerto Rico Cogeneration Plant (AESPR) is a cogeneration power plant that produces 454 MW of net electricity in its fluidized bed boiler plant in Guayama, which is sold to the Puerto Rico Electric Power Authority (PREPA). In addition, the facility commercially produces approximately 290,000 pounds per hour of pressurized steam for industrial processes of industrial clients in the area such as the neighboring Chevron Phillips Puerto Rico Core Inc. AESPR also produces fly ash, bed ash, and manufactured aggregate for commercial uses.
Project Overview
The cooling tower blowdown (CTBD) stream which contains high solids content cannot simply be discharged from the plant due to environmental regulations and therefore requires Zero Liquid Discharge (ZLD) operation. The existing process for CTBD treatment utilized a 2-stage side stream Reverse Osmosis (RO) system which reduced the wastewater volume by about 75%. Due to the problems in the upstream plant design, the RO recovery was not being achieved. Even after design reviews with other suppliers and adding of different equipment including multimedia and iron removal filters, and replacement of the RO, within a few months this retrofit experienced the same fouling and low recovery issues.
Scope of Service
The Aquatech design review revealed that a majority of the particulate in the <3 NTU clarified and filtered water was 1 micron or less, or what we called “pin floc” from the clarifier which was passing through the media filters. Aquatech conducted a pilot test with Ultrafiltration (UF) as a potential pretreatment solution. The thirty day pilot was successful and AES implemented the full scale UF which uses Hollow Fiber Membranes in 2 trains of 300 gpm each to assure the RO performance of 75% recovery. An MVC-Driven Evaporation and Crystallization system was used to achieve ZLD.
ZLD System: The reject water from the side stream RO unit is fed to the ZLD system to recycle about 99% of water as pure distillate back to the cooling tower which reduces make-up water requirements. About 70% of the total recovery is performed by the Brine Concentrator which minimizes the overall power consumption of the plant. The Brine Concentrator efficiently produces distillate through a process called Mechanical Vapor Compression (MVC) in which the energy in the evaporate is recycled with the compressor and reused for further evaporation. The Brine Concentrator uses Seeded Slurry technology to maintain a calcium sulfate seed bed to mitigate scaling of the heat transfer surface by precipitation of low solubility salts. The blowdown from the Brine Concentrator is processed by the Crystallizer which completes the water recovery and produces a solid salt cake that is dewatered and disposed to achieve ZLD. The system is designed for automatic and continuous operation, 24 hours per day.
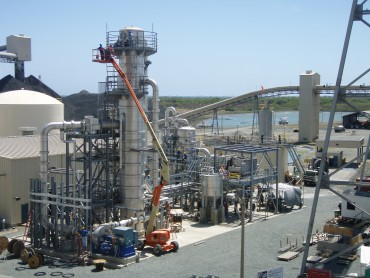
Design Water Analysis
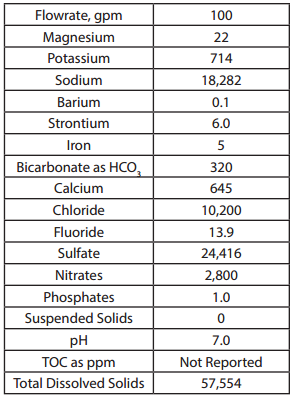
Process Flow Diagrams

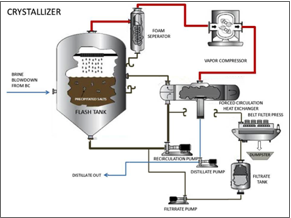