The Facility
Chemplast Sanmar Limited is the flagship company of the Sanmar Group, a leading industrial house in South India. They manufacture Chlorochemicals, PVC Resins, Caustic Soda Chlorine, Chlorinated Solvents and Silicon Wafers. The Chemplast Mettur plant uses the Cauvery River as their main fresh water source. A strong industrial growth in recent years has resulted in water scarcity in the region. Industries are also required to follow strict environmental norms for discharging effluents. The intent of a Wastewater Treatment Plant was to have complete treatment, recycle and reuse of the combined waste water streams to reduce intake from the Cauvery River while not discharging any liquid waste streams.
Project Overview
The Chemplast unit has multiple waste streams, the primary source being the Caustic soda and PVC monomer plants. The combined wastewater is heavy in contaminants like oil & grease, volatile organic compounds, and has a relatively high COD and TDS of about 10,000 mg/l. The water is potentially bio-active and also has a high fouling and scaling tendency. As an environmentally conscious corporate entity, Chemplast’s primary intent was to treat the rejects from the Reverse Osmosis (RO) system by Evaporation/Crystallization so as to achieve Zero Liquid Discharge (ZLD). They also wished to process the combined effluent to recycle the treated soft water for cooling tower make-up and other usages in the plant.
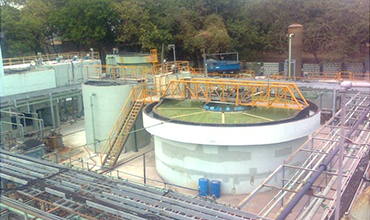
Scope of Service
Wastewater rich in BOD, COD, oil & grease etc. leads to frequent fouling due to biological and organic compounds in a RO membrane system, and is thus difficult to treat with any of the conventional effluent recycle & ZLD technologies. For Chemplast, Aquatech designed a ZLD System based on the HERO™ (High Efficiency Reverse Osmosis) technology, an advanced RO process, wherein the RO section is operated in a high pH environment. The major parameters affecting the RO system operation are kept within limits enabling high water recoveries in the range of 88 – 90%. The operating environment of the HERO™ system totally eliminates possibility of biological growth and is also resistant to fouling in the membranes, reducing the need for frequent cleaning and thus, downtime in the system. Waste streams internally produced by the plant are collected separately in a tank and pumped back into the system at an equated rate. Suitable arrangement is provided in the chamber to ensure proper mixing of the incoming streams. The HERO™ system is used to concentrate the dissolved solids in its reject stream followed by Mechanical Vapor Compression based ZLD system. The overall recovery of the complete ZLD system at Chemplast is over 97%. The combined effluent from various streams (treated Polymer, combined Monomer, Caustic plant, CMP plant, RO reject & others) shall be treated in the HERO™ system.
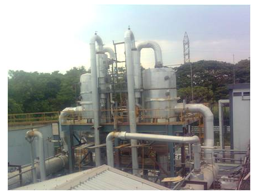
Design Water Analysis
The design analysis of the composite stream is as stated below:
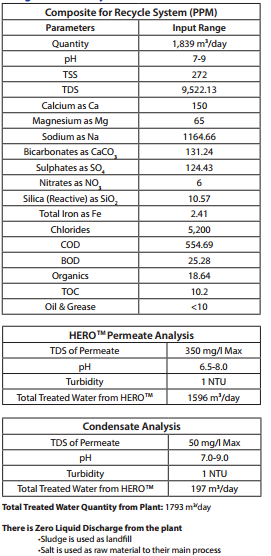
Process Flow Diagram
