The Facility
Illinois’ City of Springfield’s Dallman Power Station’s three coal-fired units and soon to be installed fourth unit are equipped with flue gas desulfurization (FGD) systems (scrubbers) to control sulfur dioxide (SO2) emissions.
Project Overview
A sharp increase in boron concentration in the FGD wastewater required that The City of Springfield Office of Public Utilities and the Illinois Environmental Protection Agency develop a boron mitigation strategy to remove the boron from the waste streams at the power generation facility. This meant including a new FGD wastewater treatment (Zero Liquid Discharge or ZLD) plant for the power plant. The elevated boron levels are caused from ammonia carryover due to the Dallman Unit’s Selective Catalytic Reduction (SCR) systems’ nitrogen removal process. In December 2005, Aquatech received a ZLD contract for the mitigation of boron from the FGD Wastewater generated at the Dallman Power Plant from the City of Springfield in Illinois.
Scope of Service
Aquatech provided a ZLD system comprising of 2 x 60% Brine Concentrators (total treated flow of 240 gpm) followed by spray dryers that will treat blowdown from the FGD scrubbers installed at the coal fired power plant.
The ZLD Evaporation System is a fully integrated, automated system incorporating a mechanical vapor compression falling film seeded slurry brine concentrator and a spray dryer system. The high purity distillate produced in this system will be used as makeup to the cooling tower or boiler feed water treatment system. The ZLD System is designed for automatic steady state operation and will minimize operator attention. The materials of construction were selected to resist corrosion and ensure a long plant life.
Features and Benefits of Aquatech Brine Concentrator in FGD Service
Optimized Materials of Construction for FGD service FGD Blowdown contains elevated levels of calcium and magnesium chloride and other similar salts. As these salts concentrate in an evaporator, they become increasingly corrosive and because of this, the evaporator materials of construction needed to be upgraded to expensive materials such as titanium and nickel based alloys. Aquatech has provided an innovative design in these brine concentrators. The design innovations limits the concentration of chlorides within levels that allow the use of more conventional materials of construction.
Another benefit of limiting the chloride concentration in the brine concentrator is in the selection of vapor compressor. The vapor compressor selected is less likely to be subjected to corrosive conditions and vibration problems that could exist in systems deployed in FGD service. Aquatech’s proprietary dual perforated plate distribution system has a proven track record of superior flow distribution of brine to the tubes practically eliminating chances of tube plugging. Unlike individual tube inserts which routinely plug up in high suspended solids brines like FGD blowdown, Aquatech’s distributor assures uniform flow of brine across the entire tube bundle and down the inside wall of each tube.
Aquatech’s design included mist eliminators that prevent droplets containing concentrated chloride salts from passing into the vapor compressor thus preventing pitting corrosion of compressor impeller and suction expansion joints. Aquatech’s unique design of the mist eliminators provides easy access and cleaning of internal sump mist eliminators eliminating the need for complicated shutdown of evaporator equipment and the need to install temporary scaffolding inside the sump.
Aquatech employs a proprietary two-stage external mist eliminator using horizontal flow chevrons for the brine concentrator which is very efficient at eliminating brine droplets which become entrained in the water vapor. The distillate produced typically contains less than 10 ppm nonvolatile solids, even with very high TDS levels in the evaporator sump. In Aquatech’s brine concentrator design for FGD service, the efficiency of the mist eliminator combined with the low chloride salt concentration maintained in the evaporator sump and high alloy construction of the vapor compressor plus the ability to rinse the compressor rotating assembly with water during operation means that corrosion potential on the vapor side of the evaporator is practically eliminated. Inspection and access to the external type mist eliminator is very straightforward as the entire mist eliminator assembly is directly accessible from the platform manway.
Design Water Analysis
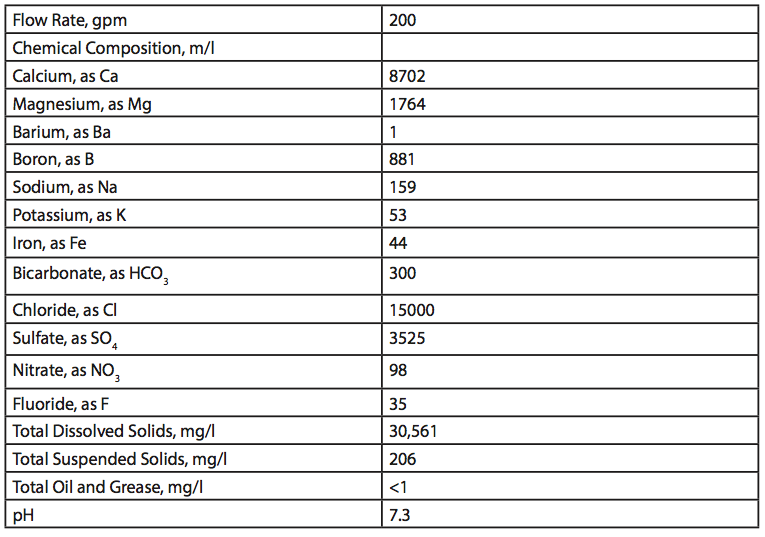
Process Flow Diagram
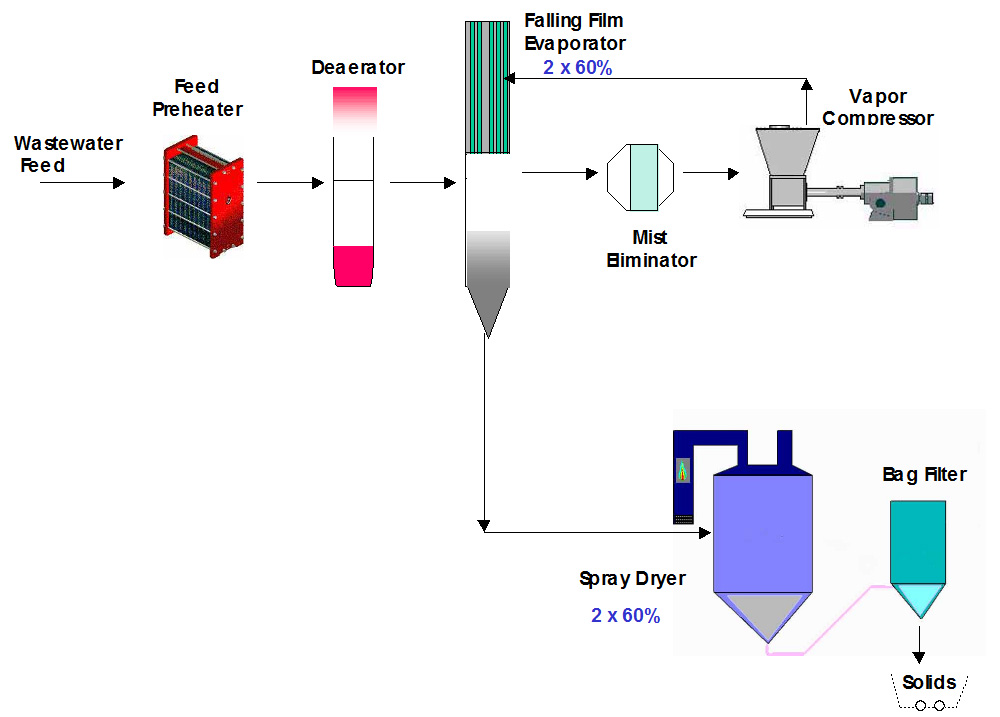