The Facility
Eagle-Picher Industries has an 8-acre hazardous waste surface impoundment pond at its Electro-Optics Division plant in Quapaw, Oklahoma.
Project Overview
By the time Eagle-Picher contacted Aquatech, the impoundment pond had been in use for more than 20 years and contained more than 5 million gallons. Environmental regulation required the plant to install a double liner in the pond. To retrofit the liner, engineers planned to concentrate the pond, dike it in the middle, pump the fluid from one side to the other, and then double-line the empty side.
The plant needed an economical way to concentrate the pond brine. The dilute (5%) calcium chloride solution includes a small amount of heavy metal salts along with some (about 400 ppm) sulfate.
Laboratory tests showed that pond brine could be evaporated to about 30% CaCl2 concentration. Recognizing that calcium sulfate has an inverse solubility curve; the presence of sulfates along with the calcium ions would likely lead to heat exchanger fouling if a typical thin-film evaporator is used.

Scope of Service
The plant installed a packaged vapor compression, forced-circulation evaporator from Aquatech. The system is capable of evaporating about 12 gpm of water and employs corrosion resistant materials of construction. The heat exchanger has titanium tubes, the flash tank is rubber lined, and the recirculation piping is fiberglass reinforced plastic. On the vapor side, the compressor is cast iron; the vapor pipe and heat exchanger shell are type 316 stainless steel.
Previous experience indicated that a vapor compression evaporator system could be used to get a higher economy than a multiple effect evaporator. Vacuum operation would permit a low operating temperature and reduce the effect of calcium sulfate’s inverse solubility. A forced circulation 60 hp axial-flow pump recirculates 4,500 gpm of concentrated liquor through the tubes of a vertical shell-and-tube heat exchanger. The pump has a mechanical seal and uses the evaporator system’s distillate water as a flush and lubricant. Heated liquid is released into the evaporator’s flash tank about 2 feet inside the vessel where it drops about 2-3 feet to the liquid level. Vapors released are compressed by a 200 hp positive-displacement, rotary-lobe compressor that discharges the vapors at about 216°F. Some of the condensate is used to desuperheat the compressed vapors before they enter the shell side of the heat exchanger. The remaining condensate is transferred to a 300,000 gallon holding tank and used in the plant as process water.
Data taken once each 8-hour shift, includes temperatures, pressures and flows at various points in the system. The evaporator runs 24 hours a day, 7 days a week. Operator attention is minimal. The pond started out at 5% concentration and was eventually concentrated to 30%. The cost of operating the system has been about $0.0125/gallon of feed based upon current electrical rates. There has not been any heat exchanger tube fouling. Calcium sulfate scale does not form on the walls of the flash tank or the connecting piping but periodic cleaning of the system alleviates the build-up. The vapor compression system has provided a reliable approach to concentrating the pond brine without the need for steam generation facilities or long runs of steam piping.
Process Flow Diagram
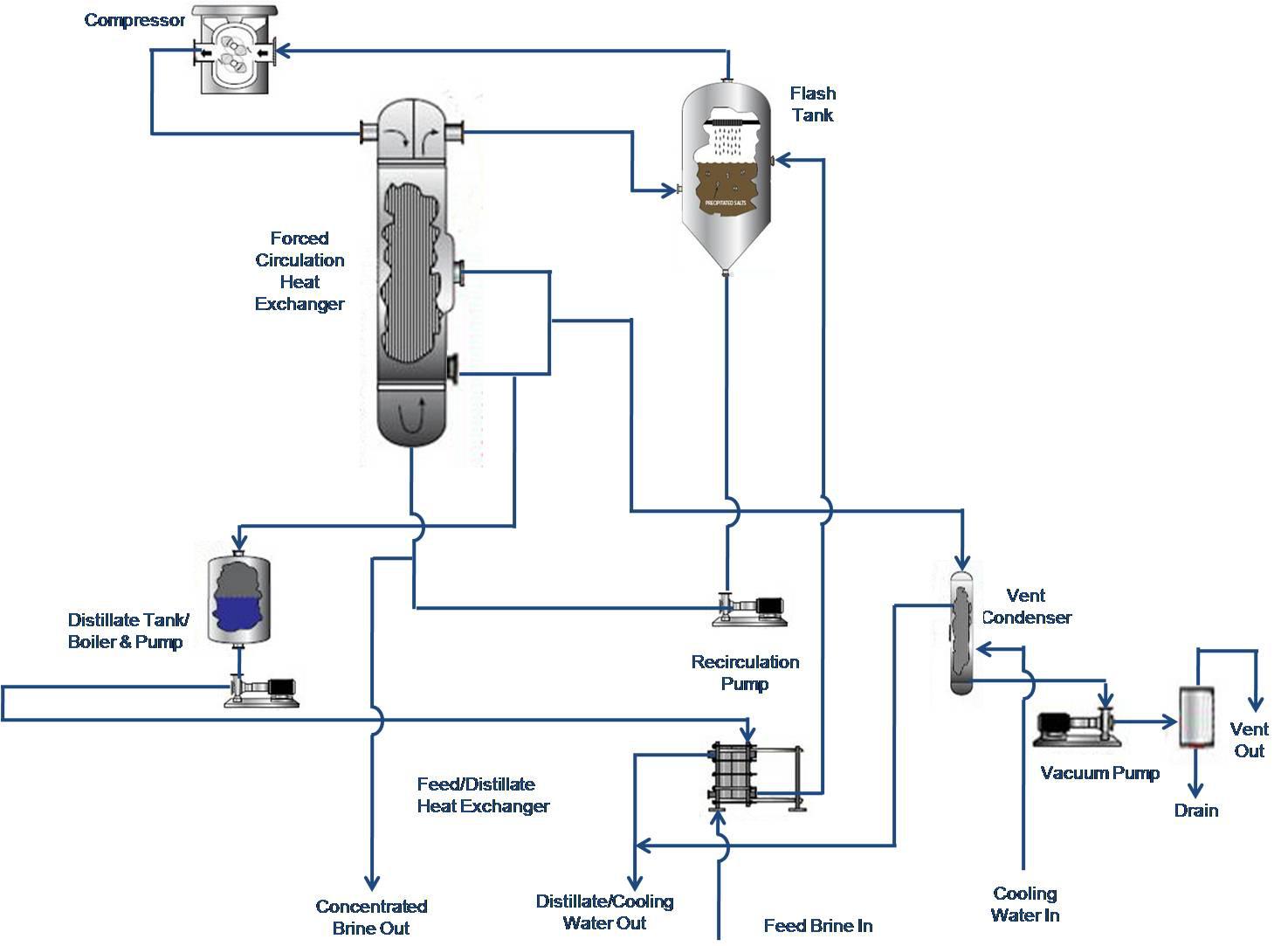