The Facility
Petroleum Development Oman (PDO) is an oil exploration and production company located in the Middle East. PDO needed high purity water to feed the oil field steam generator at their new enhanced oil recovery facility at Qarn Alam located in the Oman interior. Aquatech, together with PDO’s consultant, recognized that conventional seawater desalination equipment was unsuitable. The engineers suggested a brine concentrator to PDO, as an effective alternative.
Project Overview
The remote Qarn Alam site, located about 350 km southwest of Muscat, presented several challenging problems. Make-up water was extremely unsuitable and of limited supply. In addition, Oman’s stringent environmental constraints required careful consideration. Another important point was that the operators had limited experience with evaporation equipment, so a simple, reliable system was necessary.
Scope of Service
A vertical tube, falling film, seeded slurry, brine concentrator was designed by Aquatech to handle the calcium sulfate saturated feedwater. This high recovery (98%) vapor compression evaporator will process up to 1,650 m³/d (303 gpm) of supply water. About 1,200 m³/d (220 gpm) of the distilled water will be available as 3ppm TDS feedwater to the steam generation boiler and about 300 m³/d (55 gpm) will be available as potable water for local consumption. The waste brine (2%) is routed to a fenced solar evaporation pond, where the remaining water evaporates and dissolved solids are crystallized. To remove the salts and other impurities from the water, a vertical tube falling film seeded slurry evaporator is used. The seed crystals provide a preferential site for other crystals to attach to, which retards scaling. Upon reaching the designed operating concentration, the crystals are continuously discharged in a slurry out of the evaporator to the solar pond.
The evaporator operates on a mechanical vapor compression (MVC) cycle. After initial heating of the evaporator from boiler steam, the compressor, powered by an electric motor, provides the energy input to the evaporator. Vapor, produced from evaporation of the salty water on the inside of the tubes, is de-misted to eliminate water droplets from the vapor. This vapor flows to the compressor where compression causes the temperature of the vapor to increase, which in turn provides the evaporation driving force when the vapor is directed to the shell side of the tube bundle. The pure distillate produced from the condensed vapor is collected and fed to the boiler as makeup water.
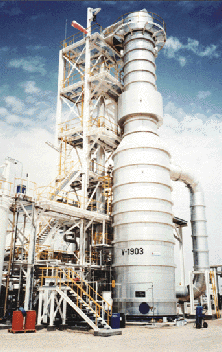
Design Water Analysis – Wastewater Chemistries
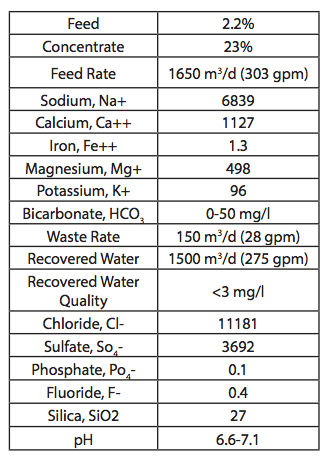
Process Flow Diagram
