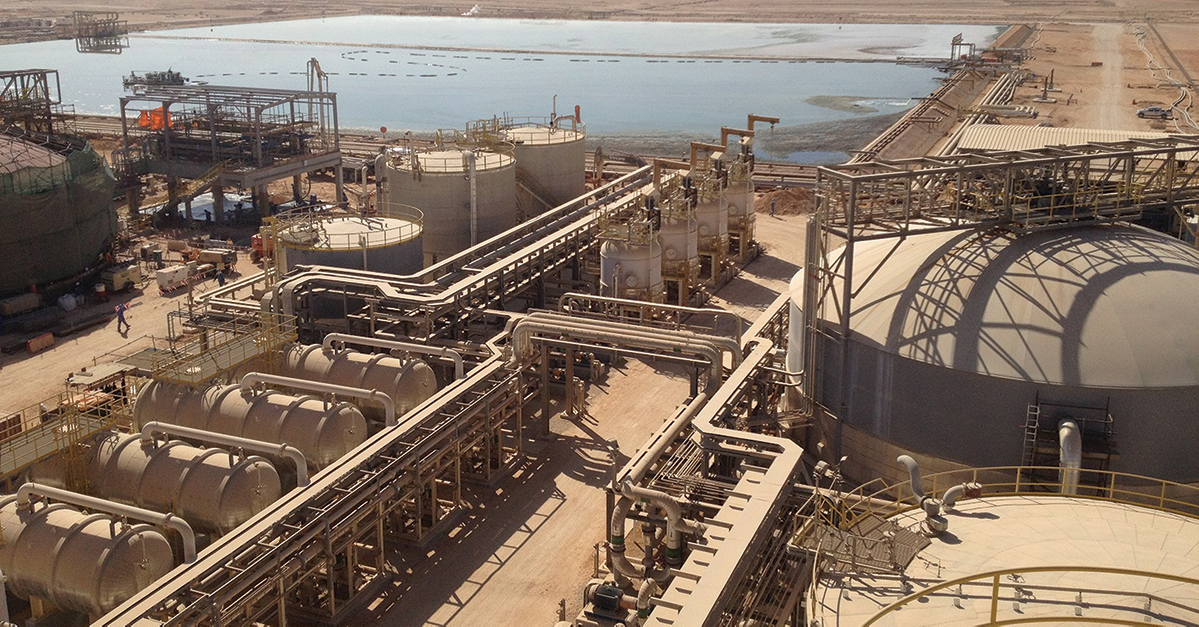
The Facility
Occidental Petroleum Corporation’s (OXY) Enhanced Oil Recovery Field is located in the south-central area of the Sultanate of Oman, approximately 660 kilometers from Muscat and 560 kilometers from Salalah. This oilfield was producing approximately 10,000 barrels of oil per day. A project was estalished to increase production to 150,000 barrels per day, to include the addition of a large scale steam flood facility for the recovery of approximately two billion barrels of oil over the life of the project. In a Steam Flood Enhanced Oil Recovery process, water is generated into steam on-site and injected in the wells (approximately 800 well pairs at this particular Oman plant). Steam injection lowers the viscosity of heavy oil suitable for extraction through the production wells. The fluid from the wells is a mixture of oil, water and gas that goes through a separation system. The separated water is called “Produced Water” and is heavily contaminated with dissolved solids and hydrocarbons. The requirements of OXY’s facility were similar to most selfsufficient oilfields in a remote desert environment having a limited fresh water source supply. This facility needed an integrated water treatment and recycling system capable of sustaining high volumes of boiler feed water to the steam generator plant that would otherwise be sourced through a local fresh water aquifer.
Scope of Service
Aquatech partnered with OXY to design and construct a fully-integrated and automated system incorporating multiple effect Mechanical Vapor Compression (MVC) brine concentrator and conventional technologies.Upon commissioning, this water treatment facility is now one of the largest produced water treatment systems in the world. Aquatech’s system consists of two phases that combine a MVC system and a conventional system to recycle and reuse approximately 90% of the produced water. The MVC system consists of seven identical trains, each having 42,860 BWPD (1,250 gpm) capacity for a Phase 1 total of 300,000 BWPD (8,750 gpm). Phase 2 consists of conventional trains producing 390,000 BWPD. The total treated water capacity of 690,000 bwpd (> 20,000 gpm) between the two phases is used as boiler feed water to the steam generator plant for this steam production and injection. Approximately 90% of the produced water is purified through the MVC system that generates a product of <10 ppm total dissolved solids content. Brine from the MVC units is collected in a settling pond and then injected into a deep well disposal system.
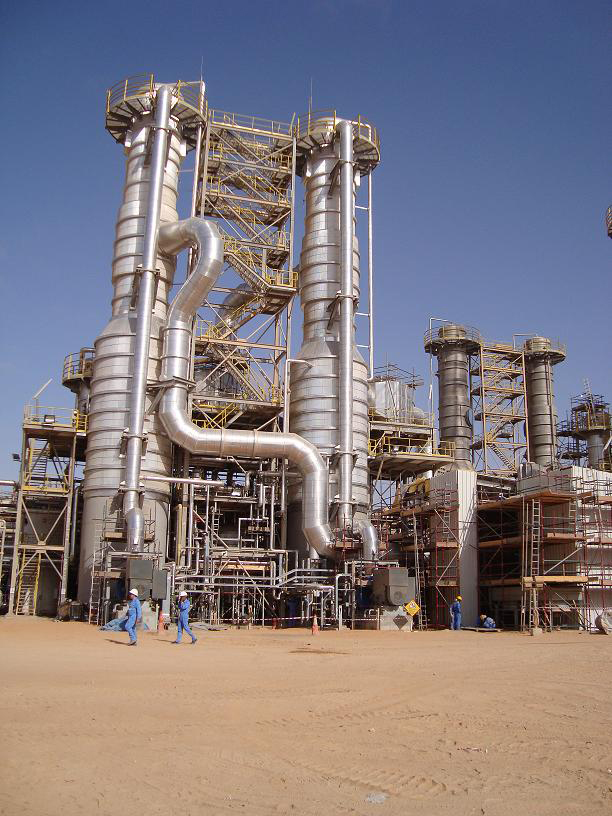
Design Water Analysis

Process Flow Diagram
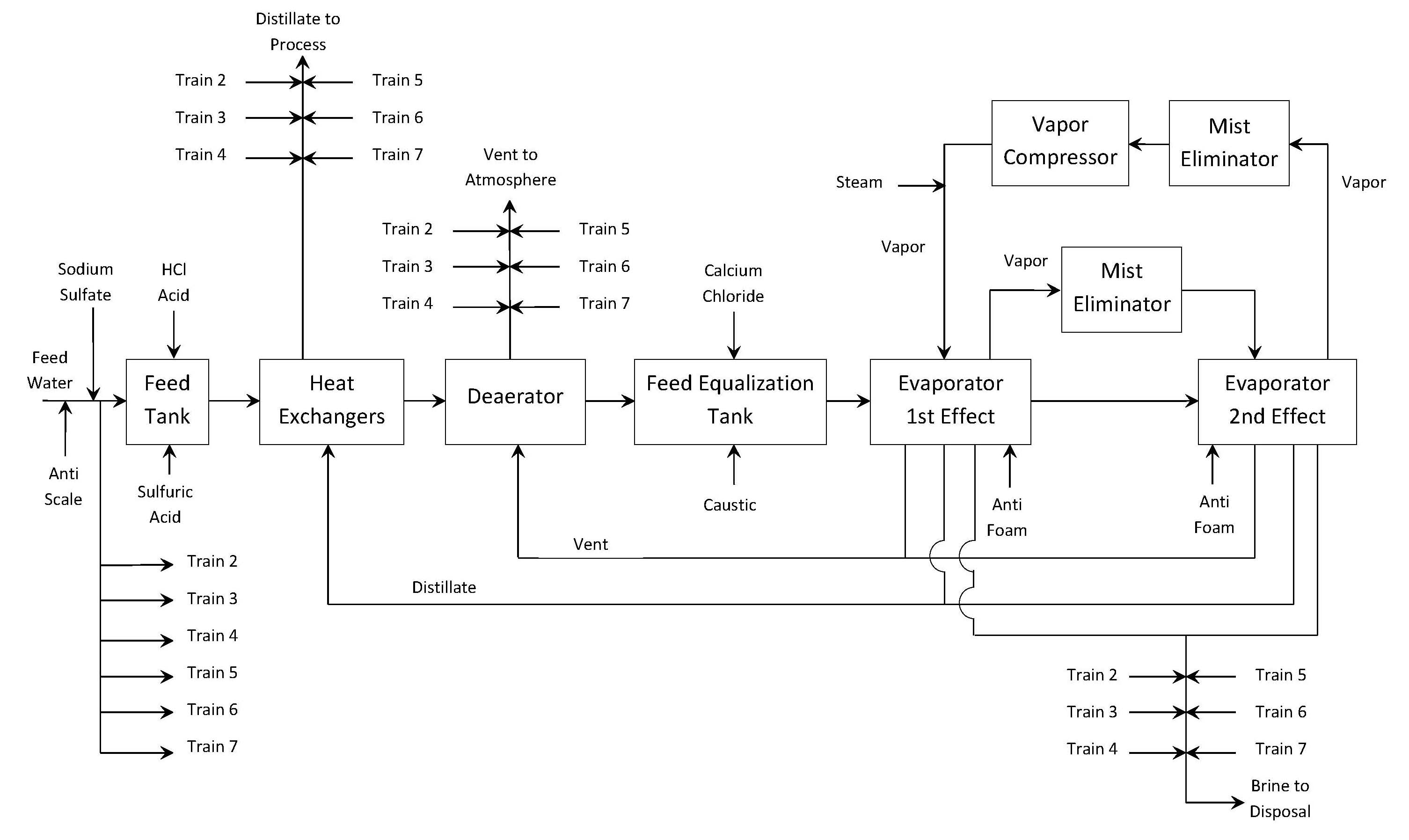