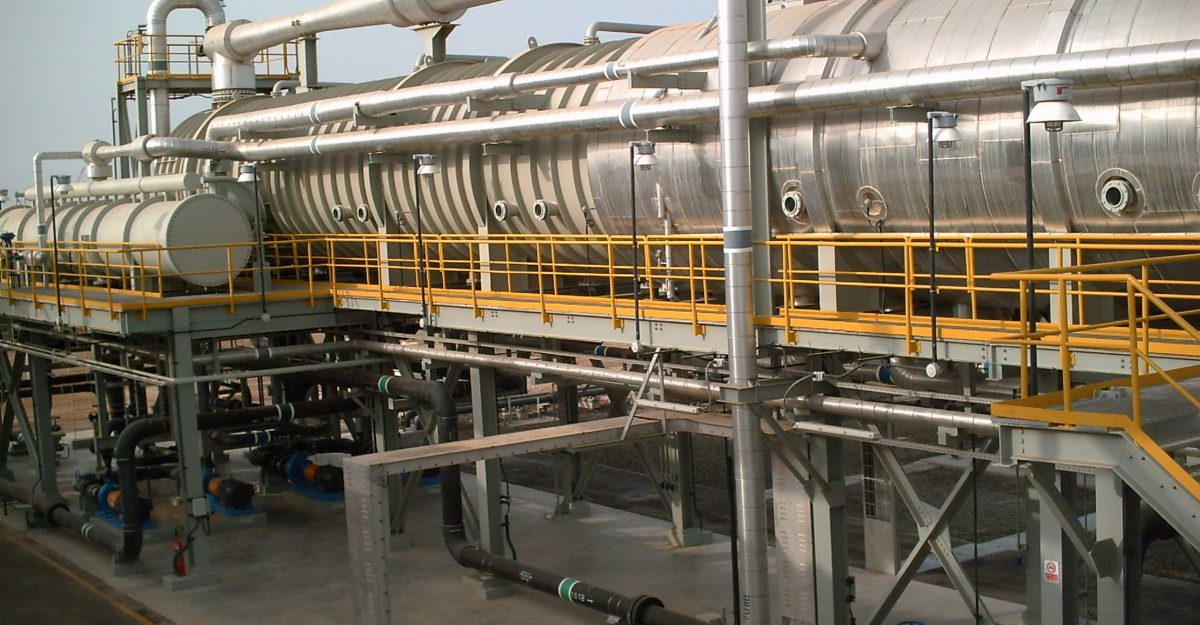
The Facility
Saudi Aramco’s RABIGH Refinery in Saudi Arabia wanted to install a facility for 10000 TPD Seawater Desalination for industrial use. The facility was supplied on a BOOT (Build Own Operate Transfer) basis.
Project Overview
The joint consortiums of SETE & Aquatech were successful in meeting the strict technical & delivery requirements of the Turnkey Desalination Plant on a BOOT basis and have been operating it consistently since. The two 5000 m³/day Multiple Effect Desalination (MED) systems are being provided for the purpose of producing Process Water and Potable Water to Saudi Aramco’s Refinery and community. The 10,000 m³/day net capacity of the Desalination Plant consists of 4000 m³/day of Process Water and 6000 m³/day of Potable Water.
The MED systems produce high purity distillate that serves as process water, and after reminineralization, as potable water. The MED systems use thermal vapor compression and are designed to the following criteria:
- Seawater temperature range from 26°C to 32°C
- Seawater TDS 41,500 ppm
- Heating source LP Steam at 3.5 kg/cm2g minimum pressure
- MP Steam to vacuum system at 17 kg/cm2g minimum pressure
- Distillate purity 5 mg/l TDS
- Condensate purity 5 mg/l TDS
- Design Capacity of 5000 m³/day each with turndown to 50% of design capacity.
The plant is designed with GOR of 8 and the achieved capacity is always more than 10000 TPD with a GOR of 8.2.
Scope of Service
Aquatech’s Multiple Effect (MED) Thermal Vapor Compression design is a multi-effect unit which incorporates SPRAY-FILM® technology, a registered trademark of Aquatech. Aquatech’s MED design is the result of over 40 years of experience in the design, manufacture, start-up and operation of MED evaporator systems worldwide.
For this system, steam or water vapor condenses inside horizontal tubes. Seawater is sprayed over the outside of the horizontal tubes and acts as a heat sink for the condensing vapor. The system operates under a vacuum with a top brine temperature below 70°C. By operating at low temperatures, the heat transfer surface is less likely to scale, and the amount of heat required to bring the incoming seawater to its boiling point is minimized. This MED plant incorporates the use of a thermo compressor to improve the thermal performance of the plant. The thermo compressor is driven by high-pressure steam, which entrains and boosts lower pressure vapors from the last effect to the moderately higher-pressure condition required in the first effect to operate the process. By recycling the lower pressure vapors from the last effect with a thermocompressor, less steam is required from an external source than if there were no thermo compressor. Part of the water vapor from the last effect is converted to liquid form in the condenser & mixed with the seawater distillate collected from all of the effects. As per the process requirements the steam condensed in the first effect is kept separated from the distillate and is reused.
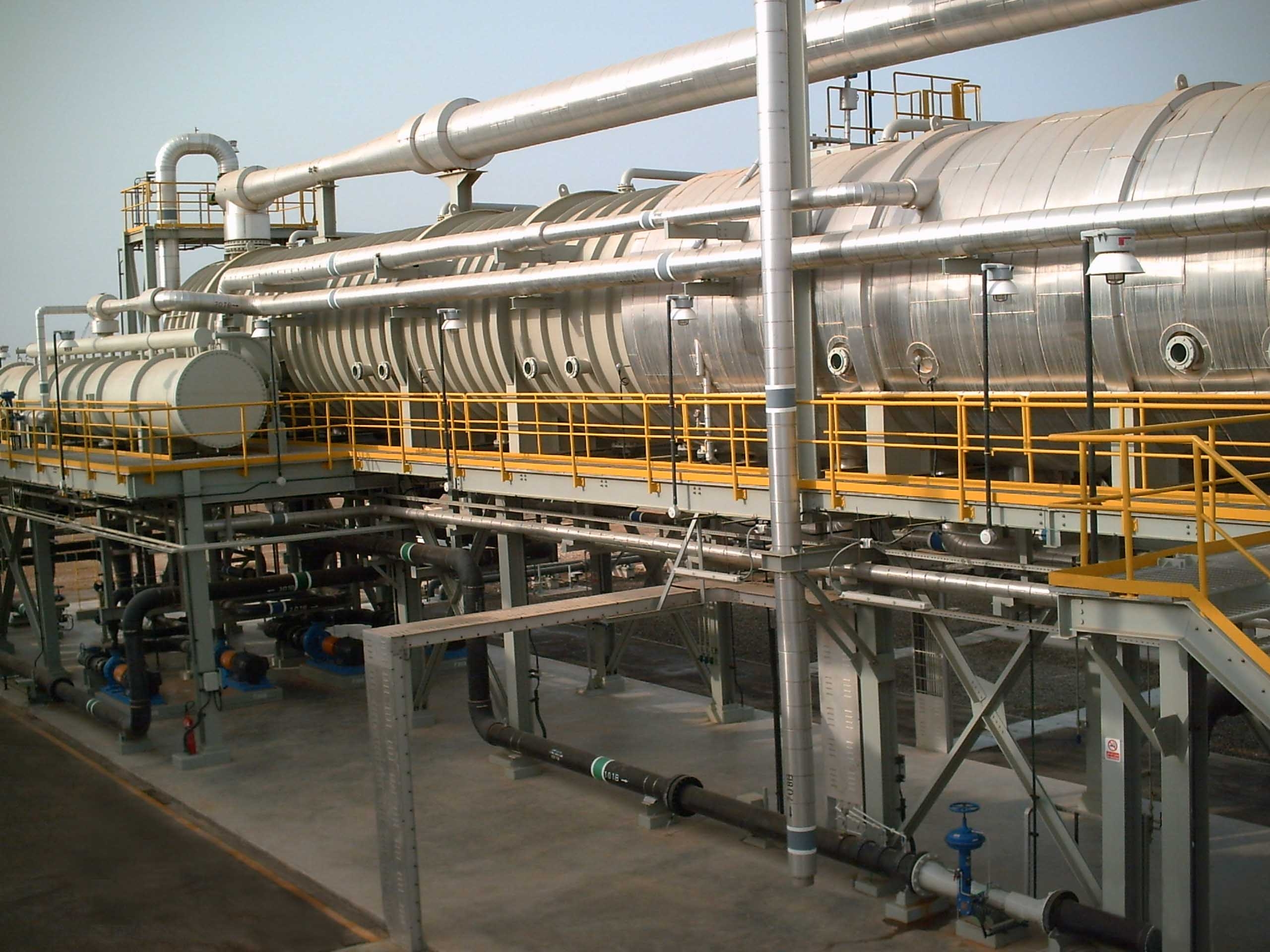
Process Flow Diagram
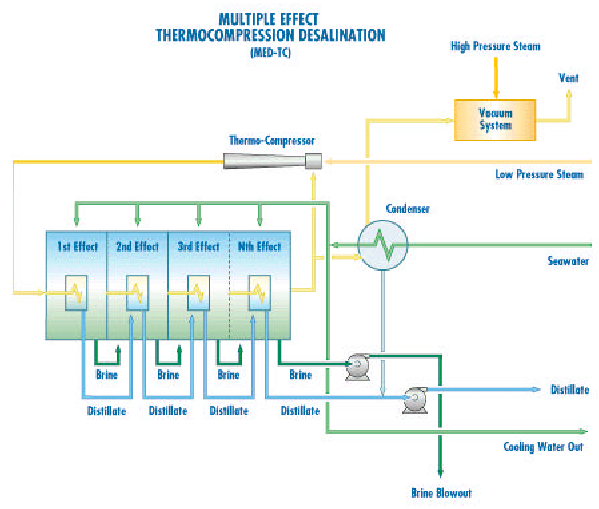